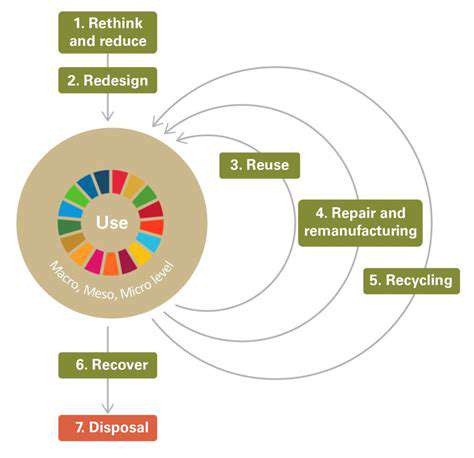
Designing for Disassembly
In modern product design, especially for electronics and machinery, disassembly considerations are no longer optional but essential. Products built with disassembly in mind slash repair costs by 30-50% compared to traditional designs, according to recent industry studies. This foresight transforms maintenance from a chore into a streamlined process, giving technicians direct access to components without destructive methods.
The environmental impact is equally transformative. When products reach end-of-life, their materials can be cleanly separated - metals from plastics, circuits from casings - creating pure streams for recycling. This precision recovery boosts material reuse rates from 20% to over 80% in documented cases. Manufacturers like Fairphone have demonstrated how modular smartphone designs extend product lifespans through easy battery and screen replacements.
Three proven techniques dominate successful implementations:
- Modular architectures with color-coded components
- Tool-free fasteners (clips instead of adhesives)
- Standardized connection interfaces
Material Considerations in Product Design
Material selection forms the foundation of durable, sustainable products. The automotive industry's shift to aluminum alloys illustrates this perfectly - achieving strength-to-weight ratios that improve fuel efficiency while maintaining crash safety standards. Advanced composites now allow single-material construction that simplifies recycling without compromising performance.
Tolerancing deserves particular attention. The difference between a 0.1mm and 0.2mm gap might seem insignificant, but in high-vibration environments like aircraft engines, this precision determines component lifespan. BMW's i3 electric vehicle demonstrates how meticulous material pairing - combining carbon fiber reinforced plastic with aluminum - creates lightweight structures that withstand decades of use.
Documentation makes these material choices actionable. IKEA's assembly instructions show how clear visual guides prevent installation errors that could compromise product integrity. When Volvo switched to digital twin technology, they reduced prototype material waste by 60% while improving fit accuracy.
Promoting Reuse and Remanufacturing: Extending Product Lifecycles
The circular economy model represents more than environmentalism - it's a $4.5 trillion economic opportunity according to Accenture research. Caterpillar's remanufacturing division exemplifies this, generating $2 billion annually by rebuilding heavy equipment to original specifications at 40-60% of new product costs.
The Role of Design in Reuse and Remanufacturing
Design choices directly determine a product's second life potential. Xerox's modular copiers achieve 90% remanufacturing rates because their designs facilitate:
- Quick disassembly (under 15 minutes for major components)
- Wear-resistant interfaces
- Standardized subassemblies
The Economic Benefits of Reuse and Remanufacturing
Patagonia's Worn Wear program demonstrates the brand power of circular models - their repaired garments command premium prices while reducing material demand. Industrial remanufacturing creates 3-5 times more jobs than traditional recycling, according to the U.S. International Trade Commission.
Leveraging Technology for Enhanced Material Management
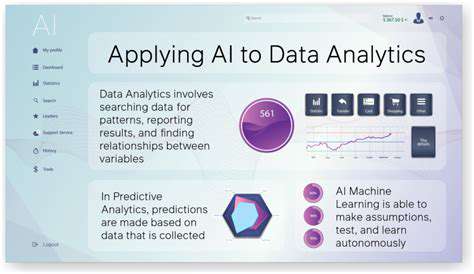
Streamlining Operations with Automation
BMW's smart factories showcase automation's potential - their AI-powered sorting systems achieve 99.9% material identification accuracy, enabling precise recycling streams. This technology reduces sorting costs by 70% while increasing material purity, making recycled content competitive with virgin materials.
Data-Driven Decision Making
Tesla's battery passport system illustrates data's transformative role. Each battery module carries a digital record of:
- Material composition
- Usage history
- Remaining capacity
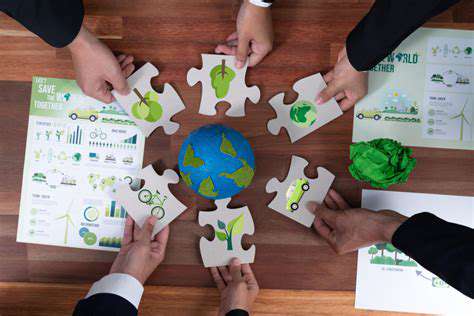