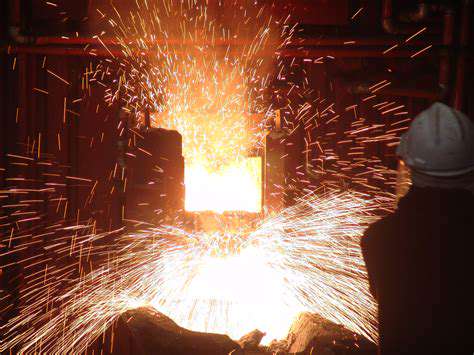
Fundamentals of Pyrometallurgical Processes
Pyrometallurgical techniques are a crucial aspect of extractive metallurgy, encompassing a wide range of high-temperature processes designed to extract metals from their ores. These processes rely on chemical reactions driven by heat to achieve the desired separation and purification. Understanding the fundamental principles behind these reactions is essential for optimizing process efficiency and controlling product quality. This includes manipulating variables like temperature, pressure, and the presence of other chemical species to facilitate the desired chemical transformations.
The selection of a particular pyrometallurgical technique depends heavily on the specific ore composition and the desired metal product. For instance, some ores require pre-treatment steps like roasting or calcination to improve the subsequent reduction process. Different techniques are tailored to different metal types and to varying degrees of purity needed in the final product. This careful consideration of variables is paramount to achieving successful outcomes.
Applications and Advantages of Pyrometallurgy
Pyrometallurgy offers several advantages over other metallurgical methods. One key advantage is its ability to handle a wide variety of ore types, including those with complex compositions. This makes it a versatile option for various mining operations. Furthermore, pyrometallurgical processes are often more cost-effective, especially when dealing with ores that are difficult to treat using other methods.
A significant application of pyrometallurgy is in the production of ferrous metals, such as iron and steel. The high temperatures involved in these processes allow for the efficient reduction of iron oxides and the subsequent refining of the resulting metal. This is a critical aspect of the steel industry and has been instrumental in powering industrial development throughout history. Another important application is in the processing of non-ferrous metals, such as copper, lead, and zinc, though the specific techniques used vary widely based on the exact ore characteristics and the desired product.
The use of pyrometallurgical methods is also increasingly important in the treatment of secondary materials, such as scrap metals. This recycling process minimizes environmental impact by reducing the need for primary extraction from virgin ores. This aspect of sustainability is crucial as resource depletion is an ongoing concern, making pyrometallurgy a vital tool for the future.
Pyrometallurgical techniques often produce valuable byproducts, which can be further processed or sold, adding a significant economic benefit to the overall process. This added value, coupled with the ability to handle a wide range of ore types, makes pyrometallurgy a prominent choice for many mining operations.
The high temperatures involved in pyrometallurgy can also facilitate the removal of impurities from the metal product. This feature enhances the purity and quality of the resulting metal, making it suitable for a wide range of applications.
Mechanical Separation and Pre-treatment: Initial Stages of Recycling
Mechanical Separation
Mechanical separation is a crucial initial step in EV battery recycling. This process involves physically separating various components of the disassembled battery pack. Different materials, such as metals, plastics, and composites, are separated using techniques like crushing, grinding, and screening. This meticulous initial stage ensures that valuable materials are isolated for subsequent processing, maximizing the recovery of reusable components and minimizing contamination.
The efficiency of mechanical separation directly impacts the overall success of the recycling process. Precise sorting and separation techniques are vital to avoid cross-contamination of different materials, which can significantly affect the quality of the recovered materials and the subsequent processing steps. Careful consideration of the specific battery designs and materials used is essential for optimizing the mechanical separation process.
Pre-treatment Processes
Pre-treatment processes are essential for preparing the separated components for further processing and maximizing material recovery. These steps often involve cleaning, washing, and further processing to remove impurities and contaminants. This process is critical for removing any residual materials, such as electrolytes, which could hinder the subsequent chemical separation and recovery processes. Thorough cleaning ensures that the materials are in a suitable state for further treatment and that valuable components are not lost due to contamination.
One crucial aspect of pre-treatment is the removal of hazardous materials, such as heavy metals. Proper handling and disposal of these hazardous materials are paramount for environmental protection and worker safety. Specialized equipment and procedures are employed to ensure safe and efficient removal of these hazardous materials, preventing potential environmental damage and health risks.
Chemical Separation
Chemical separation techniques are employed to further extract and isolate valuable components from the pre-treated materials. These methods often involve the use of specific chemicals or processes to dissolve or selectively extract targeted materials. For example, different chemical processes are used to extract valuable metals like cobalt and nickel from the battery components. This step is crucial for maximizing the recovery of valuable materials, and the choice of chemical methods is crucial to ensure efficiency and minimize environmental impact.
Material Recovery and Purification
Following chemical separation, the recovered materials undergo purification processes to achieve the desired purity levels. This crucial step involves removing any remaining impurities and contaminants to ensure the quality and usability of the recovered materials. The recovered materials are often refined and further processed to meet the specifications required for various applications. This process might involve different techniques, including further chemical treatment, physical separation, or other sophisticated methods to achieve the desired purity levels. These purified materials can then be reused in new battery production or other applications.