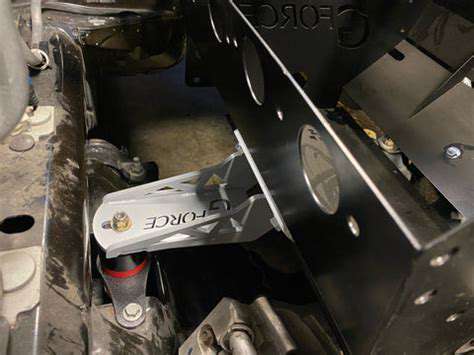
Engine Mount Importance
While often overlooked, engine mounts serve as the silent workhorses that keep your vehicle running smoothly. These components act as a buffer between your engine and chassis, absorbing the constant vibrations generated during operation. Without them, every drive would feel like riding a jackhammer.
The difference between a well-maintained engine mount system and a failing one is like night and day - you'll immediately notice the improvement in ride quality when they're functioning properly. Mechanics frequently see vehicles where neglected mounts have caused collateral damage to adjacent components, turning what could have been a simple repair into an expensive overhaul.
Types of Engine Mounts
Automakers employ different mount designs based on vehicle purpose and engine characteristics. Performance cars often use stiffer mounts to maintain precise engine positioning during aggressive driving, while luxury vehicles prioritize vibration isolation for passenger comfort. The choice of material and design significantly impacts how the vehicle feels and performs.
Rubber mounts remain popular for their cost-effectiveness and decent vibration absorption, though they tend to degrade faster than other types. More sophisticated designs incorporate hydraulic fluid or pressurized air chambers to provide superior isolation. When selecting replacements, matching the original specifications is crucial - the wrong type can create more problems than it solves.
Engine Mount Failure Symptoms
Failing mounts announce their condition through several telltale signs. Drivers might notice the steering wheel shaking more than usual, especially when stopped at traffic lights. The vibrations often intensify when accelerating or going uphill as the engine works harder against compromised mounts.
One particularly concerning symptom is visible engine movement - if you can see the engine rock significantly when revving in neutral, your mounts likely need immediate attention. Strange clunks when shifting gears or hitting bumps also frequently point to mount issues. These symptoms shouldn't be ignored, as they often worsen quickly.
Engine Mount Replacement and Maintenance
Proactive mount maintenance can prevent numerous drivability issues. During routine service, technicians should inspect mounts for cracking, separation, or excessive compression. Many manufacturers recommend replacement around 60,000-100,000 miles, but harsh driving conditions may accelerate wear.
Replacing mounts requires careful attention to detail - improper installation can leave the engine misaligned, causing premature wear on drivetrain components. While some DIYers tackle this job, the precision required makes professional installation worthwhile for most vehicle owners. Quality replacement parts also make a significant difference in longevity and performance.
Maintaining Engine Alignment: A Critical Role
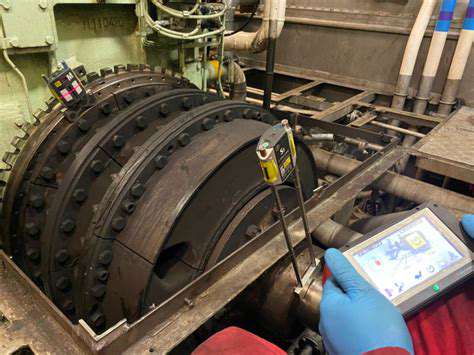
Maintaining Engine Alignment: Importance
Proper engine alignment affects nearly every aspect of vehicle operation. When components are properly aligned, power transfers efficiently from the engine to the wheels without unnecessary friction or vibration. This not only improves performance but also extends the life of expensive drivetrain components.
Misalignment often develops gradually, making it easy to overlook until damage becomes severe. The cumulative effect of small misalignments can lead to oil leaks, excessive bearing wear, and even catastrophic engine failure in extreme cases. Regular alignment checks are far cheaper than repairing the damage caused by neglect.
Visual Inspection Techniques
Start alignment checks with a simple visual assessment. Look for uneven gaps between engine components or signs that parts are rubbing where they shouldn't. Pay particular attention to accessory belts - misalignment often shows up as uneven wear patterns. A flashlight helps spot subtle issues that might be missed in poor lighting.
Measuring Engine Alignment
Precision measurements transform guesswork into actionable data. Dial indicators mounted to stationary points can detect movement as small as thousandths of an inch. Laser alignment tools provide even greater accuracy for critical applications. These measurements establish baseline data for comparison during future inspections.
Causes of Engine Misalignment
Impact damage from accidents or hitting large potholes represents the most obvious cause, but subtler factors also contribute. Improperly torqued fasteners during repairs can gradually pull components out of alignment as they settle. Even normal wear on motor mounts and bushings allows enough movement to create problems over time.
Corrective Actions
Addressing misalignment ranges from simple adjustments to major repairs. Sometimes loosening mounting bolts and gently repositioning components solves the issue. More severe cases might require machining mounting surfaces or replacing warped components. Always verify corrections with follow-up measurements.
Preventive Maintenance Strategies
Build alignment checks into regular maintenance intervals. Documenting measurements creates a valuable history that helps spot developing issues before they become serious. When working on the engine, use torque wrenches and follow tightening sequences precisely to maintain proper alignment.
The Role of Professional Technicians
While basic checks are within reach of most owners, complex alignment issues demand specialized tools and expertise that only professional shops possess. Their precision equipment can detect problems invisible to the naked eye, and their experience helps distinguish normal variations from actual faults.
Types of Engine Mounts and Their Applications
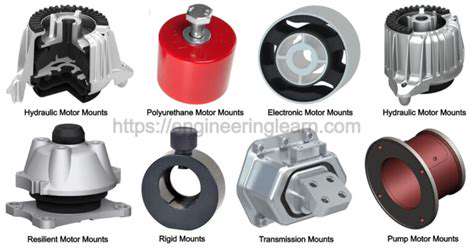
Engine Mount Types: A Comprehensive Overview
Modern vehicles use increasingly sophisticated mounting systems tailored to specific performance goals. The evolution from simple rubber blocks to computer-controlled active mounts reflects the automotive industry's ongoing pursuit of refinement. Understanding these options helps make informed maintenance decisions.
Rubber Mounts: The Foundation of Vibration Control
Traditional rubber mounts continue to dominate the market due to their simplicity and cost-effectiveness. The best designs incorporate different rubber densities within a single mount to handle various vibration frequencies. Some include voids or chambers that collapse under heavy loads to provide progressive damping characteristics.
While generally durable, rubber mounts face challenges in extreme temperatures. Cold weather makes the rubber stiffer, reducing effectiveness, while heat accelerates chemical breakdown. High-quality rubber compounds and proper sizing help mitigate these limitations.
Hydro-Pneumatic Mounts: A Sophisticated Approach to Vibration Dampening
These advanced mounts use fluid dynamics to provide frequency-sensitive damping. The liquid inside flows through precisely calibrated passages, responding differently to various vibration frequencies. Some designs incorporate electronically controlled valves that adjust damping in real-time based on driving conditions.
The complexity brings both benefits and drawbacks. While offering superior isolation, these mounts cost significantly more and may require specialized service procedures. They're most common in premium vehicles where NVH (noise, vibration, harshness) standards are exceptionally high.
Metal Mounts: Strength and Durability in Action
Metal mounts excel in applications where minimizing movement takes priority over vibration isolation. Racing applications frequently use solid aluminum or steel mounts to maintain precise engine positioning during extreme maneuvers. The tradeoff comes in increased vibration transmission, which most street drivers find unacceptable.
Some designs attempt to balance these factors by using metal with integrated rubber or polyurethane bushings. These hybrid approaches provide better isolation than solid metal while maintaining greater control than pure rubber mounts. The right choice depends entirely on the vehicle's intended use.