Advanced Monitoring Techniques: Predictive Analytics and Data Logging
Predictive Analytics for EV Battery Health
Predictive analytics plays a crucial role in extending the lifespan and ensuring optimal performance of EV batteries. By analyzing historical data, including charging patterns, temperature fluctuations, and usage profiles, sophisticated algorithms can identify potential degradation trends and predict future battery performance. This proactive approach allows for timely interventions and maintenance, preventing unexpected battery failures and maximizing the overall operational efficiency of the electric vehicle. Such predictive models can be trained to recognize subtle patterns indicative of stress or degradation, allowing for preventive measures to be taken before the battery experiences significant performance loss.
The key benefit of predictive analytics is its ability to forecast potential issues. Instead of reacting to failures, maintenance teams can proactively address emerging problems, potentially extending battery life by years and significantly reducing repair costs. This proactive approach is particularly valuable in the EV industry, where battery degradation can impact the overall range and performance of the vehicle, impacting customer satisfaction and operational costs.
Data Logging for EV Battery Performance
Comprehensive data logging is essential for understanding the intricate relationship between various factors and EV battery health. Detailed logs capture crucial parameters such as voltage, current, temperature, and charging cycles. By meticulously recording these parameters over time, manufacturers and users gain valuable insights into battery behavior under different operating conditions. This data forms the foundation for developing effective predictive models and allows for the identification of anomalies and potential degradation patterns.
The systematic logging of data, coupled with careful analysis, offers a substantial advantage in understanding battery performance. This information facilitates the development of more resilient battery designs and improved battery management systems. Data logs provide a historical record, enabling researchers and engineers to trace the evolution of battery health and identify correlations between different operating conditions and degradation rates.
Real-Time Monitoring and Alerting Systems
Real-time monitoring systems are becoming increasingly important in the management of EV batteries. By continuously tracking key parameters, these systems can identify unusual patterns and potential issues immediately. This enables proactive intervention, preventing further damage and ensuring optimal battery performance. Real-time data feeds allow for immediate alerts, notifying maintenance personnel of potential problems, facilitating prompt diagnosis and mitigation strategies. This rapid response capability is crucial for minimizing operational downtime and maximizing battery efficiency.
These systems can be integrated with various components of the EV, including the charging infrastructure, to provide a comprehensive overview of battery health. Real-time alerts provide immediate notification of critical issues, empowering technicians to address problems before they escalate. This proactive approach translates to improved vehicle reliability and a superior user experience.
Advanced Diagnostic Tools for Battery Health
Sophisticated diagnostic tools are crucial for a deeper understanding of EV battery health. These tools go beyond basic measurements, offering detailed analyses of internal battery conditions. This detailed information enables more accurate assessments of battery degradation, identifying specific cell or module issues. Advanced tools allow for a more precise diagnosis of potential problems, enabling targeted interventions, which are essential for maintaining optimal performance. The ability to pinpoint specific issues allows for targeted solutions, ultimately maximizing the lifespan and performance of EV batteries.
The Importance of Regular Maintenance and Professional Inspections
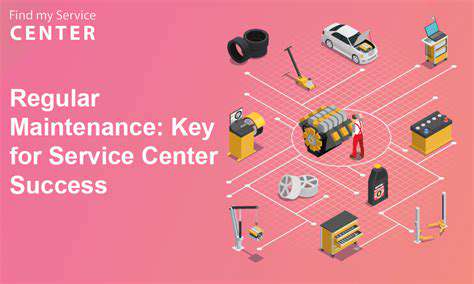
Preventive Measures for Optimal Performance
Regular maintenance is crucial for ensuring that equipment operates at peak efficiency and longevity. Properly maintained systems experience fewer breakdowns, leading to reduced downtime and significant cost savings in the long run. Preventive maintenance strategies are proactive, rather than reactive, and help to anticipate potential issues before they escalate into major problems. This proactive approach extends the lifespan of the equipment and prevents costly repairs.
Routine checks and replacements of parts, such as filters and lubricants, are essential components of a comprehensive preventive maintenance program. These simple tasks can prevent more complex issues from arising and keep your equipment running smoothly. By investing in regular maintenance, you're investing in the future of your operations.
Addressing Potential Issues Early
Identifying and addressing potential issues early on is a key aspect of regular maintenance. This proactive approach allows you to nip problems in the bud, preventing them from escalating into significant breakdowns and costly repairs. By catching small problems early, you can avoid major disruptions to production schedules and maintain a consistent workflow.
Regular inspections can often reveal minor problems that, if left unaddressed, could lead to more significant issues. This includes things like loose connections, wear and tear on components, and early signs of corrosion. These small issues are easier and cheaper to fix than major breakdowns.
Minimizing Downtime and Improving Productivity
Regular maintenance significantly reduces downtime by proactively addressing potential issues. Minimizing downtime translates directly to increased productivity and efficiency. Reduced downtime translates directly to a higher return on investment. By implementing a well-defined maintenance schedule, you can minimize unexpected equipment failures.
Predictive maintenance, a part of regular maintenance, allows you to anticipate potential failures. This proactive approach to maintenance reduces unforeseen downtime, enabling your equipment to operate consistently and maximizing its output. This leads to improved productivity and a more efficient workflow.
Cost Savings in the Long Run
While regular maintenance may seem like an additional expense, it's a crucial investment that leads to significant cost savings in the long run. By preventing major breakdowns, you avoid the high costs associated with repairs and replacements. This includes the cost of labor, parts, and potential lost production time.
The cost of a single major breakdown can easily outweigh the expense of a comprehensive maintenance program. Regular maintenance is a wise investment that protects your equipment, reduces your overall costs, and enhances your bottom line.
Safety and Compliance Considerations
Regular maintenance plays a critical role in ensuring the safety of personnel and equipment. Properly maintained equipment is less prone to malfunctions and hazards. This also contributes to compliance with industry standards and regulations. Ensuring safety is paramount for any operation.
Regular maintenance inspections help identify potential safety hazards and allow for corrective actions to be implemented. This proactive approach minimizes the risk of accidents and injuries, protecting your employees and ensuring compliance with safety regulations.
Improving Equipment Lifespan and Reliability
Regular maintenance significantly extends the lifespan of equipment. By addressing wear and tear, and potential problems early on, you can maintain the reliability of your equipment. Regular maintenance procedures greatly enhance the equipment's lifespan and reliability. This translates to reduced replacement costs and a more stable operating environment.
Maintaining equipment in good condition ensures it can perform its intended function reliably and effectively. This leads to improved efficiency and fewer unplanned interruptions to your operations. Proactive maintenance is an investment in the future of your operational efficiency.
Environmental Impact of Neglect
Neglecting regular maintenance can have a significant negative impact on the environment. Unmaintained equipment often leads to increased energy consumption and potentially harmful emissions. This includes things like leaks and inefficient operation. Neglecting maintenance can lead to significant environmental harm.
Implementing regular maintenance procedures helps optimize energy usage and reduce environmental impact. Properly maintained equipment operates more efficiently, consuming less energy and emitting fewer pollutants. Environmental consciousness should be a key factor in any maintenance policy.