Minimizing Environmental Impact in Raw Material Acquisition
The journey toward sustainability begins with how we source our raw materials. Ethical procurement isn't just a trend - it's a fundamental shift in how responsible businesses operate today. Forward-thinking companies now meticulously evaluate their suppliers' environmental practices, looking beyond mere compliance to genuine ecological stewardship. This means choosing partners who actively prevent deforestation, protect waterways, and preserve natural habitats.
The materials themselves deserve equal scrutiny. Innovative alternatives like recycled plastics or plant-based composites often outperform traditional options, not just environmentally but sometimes functionally too. Some automotive manufacturers now use mushroom-based insulation that's lighter and more sustainable than petroleum-based alternatives. Continuous R&D investment in these areas yields solutions we haven't even imagined yet.
Optimizing Manufacturing Processes for Reduced Waste
Modern factories are rewriting the rules of production. The most advanced facilities now operate like living organisms, where waste from one process becomes raw material for another. Japanese automakers have perfected this approach - their plants reuse 99% of wastewater and recycle over 90% of production scraps. Digital twins (virtual factory models) allow engineers to simulate processes and eliminate waste before physical production begins.
Reducing Energy Consumption During Production
The energy transformation in manufacturing is accelerating. Solar-powered factories aren't futuristic concepts anymore - they're today's reality. In Germany, some industrial plants generate surplus renewable energy they feed back into the grid. Smart sensors and AI-driven energy management systems can cut power usage by 30% or more by optimizing equipment operation in real-time.
Minimizing Water Usage and Pollution
Water stewardship separates truly sustainable operations from those merely claiming environmental responsibility. Closed-loop water systems have become the gold standard, with some textile manufacturers now recycling the same water up to ten times through advanced filtration. One denim producer developed a laser-finishing technique that uses 90% less water than traditional stone-washing methods.
Promoting Responsible Waste Management and Disposal
The circular economy is revolutionizing waste management. What was once trash is now recognized as misplaced resources. Electronics manufacturers have made remarkable progress, with some achieving 98% recycling rates for smartphones. Biodegradable packaging made from seaweed or agricultural waste decomposes in weeks rather than centuries, offering real solutions to our plastic crisis.
Enhancing Transparency and Collaboration
True sustainability requires tearing down information silos. Blockchain technology now enables unprecedented supply chain visibility, allowing consumers to trace a product's entire journey with a smartphone scan. Industry consortiums share best practices openly, recognizing that environmental challenges demand collective solutions. This collaborative spirit is driving innovations that benefit entire sectors simultaneously.
Promoting Labor Rights and Fair Wages Across the Supply Chain
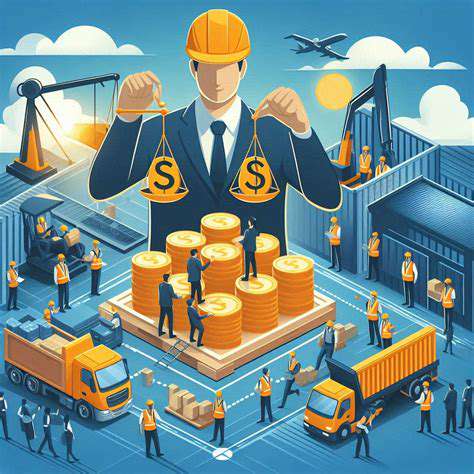
Promoting Fair Wages
Compensation practices reflect a company's values more accurately than any mission statement. Living wages transform workforces, turning struggling employees into engaged partners. Research consistently shows that fair pay reduces turnover by 50% or more while increasing productivity. Some apparel brands now publish their wage calculations openly, demonstrating how worker pay aligns with local living costs.
Protecting Workers' Rights
Fundamental rights form the foundation of ethical employment. The most successful factories empower their workers as stakeholders, not just labor inputs. In Bangladesh, worker-led safety committees have reduced garment factory accidents by over 70% since 2013. Digitized grievance systems now give voice to employees at all levels, with AI-powered translation breaking down language barriers in multinational operations.
Enhancing Workplace Safety
Safety innovations are saving lives across industries. Smart wearables now monitor factory conditions in real-time, alerting managers to potential hazards before accidents occur. Exoskeletons reduce injury rates in logistics by 60% by supporting workers handling heavy loads. The most progressive companies view safety spending not as a cost but as an investment in their most valuable asset - their people.
Promoting Collective Bargaining
Labor relations are evolving beyond adversarial negotiations. Co-determination models, where workers hold board seats, create remarkable alignment between employee and corporate interests. German companies using this approach consistently outperform competitors in both productivity and employee satisfaction. Digital platforms now enable remote workers to participate fully in union activities, expanding collective bargaining's reach.
Addressing Discrimination and Harassment
Inclusion is the new imperative for modern workplaces. Behavioral analytics tools now help identify and address toxic patterns before they escalate. One Fortune 500 company reduced harassment reports by 80% after implementing AI-powered communication monitoring (with strict privacy protections). Cultural competency training has moved beyond compliance to become a strategic advantage in global markets.
Improving Working Conditions
The future of work prioritizes human well-being. Ergonomic enhancements boosted productivity by 25% in one auto plant study, proving comfort and efficiency go hand-in-hand. Some tech companies now use environmental sensors to automatically adjust lighting and temperature for optimal cognitive performance. The best workplaces feel designed for humans first, processes second.
Encouraging Education and Training
Continuous learning defines competitive workforces today. AR training simulations cut new employee ramp-up time by 40% in manufacturing trials. One retailer's education reimbursement program generated a 300% ROI through improved retention and performance. Forward-thinking companies build learning cultures where skill development is woven into daily work, not just occasional seminars.
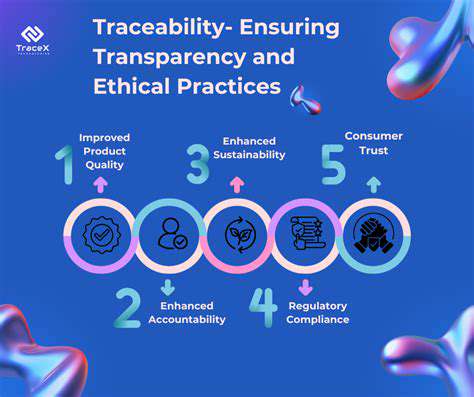
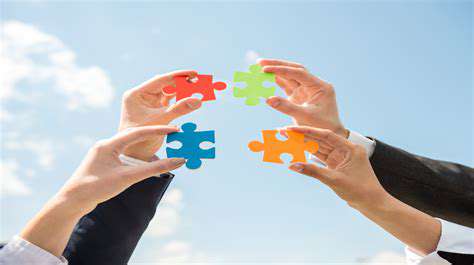