Understanding the Basic Function
Universal joints, though frequently overlooked in drivetrain systems, serve as the backbone for seamless power transfer between misaligned shafts. Their ingenious design accommodates substantial angular variations, making them indispensable in applications from automotive to agricultural equipment. This adaptability is the linchpin for maintaining uninterrupted power flow while preventing excessive wear on interconnected parts. Vehicles, in particular, rely on this flexibility to harmonize wheel and suspension movements with the drive shaft's rotation.
Picture a car navigating a sharp turn. Absent a universal joint, the drive shaft would endure immense stress, likely failing under the strain of angular displacement. The joint's clever articulation absorbs these dynamic changes, guaranteeing consistent torque delivery regardless of the vehicle's orientation. This principle extends far beyond automobiles, forming the mechanical foundation for countless industrial applications.
The Mechanics of Flexibility
The universal joint's magic resides in its yoke configuration - paired intersecting shafts linked by precisely engineered yokes. Manufacturers typically forge these components from high-grade metal alloys, selecting materials for their exceptional resilience under operational stresses. The joint's true brilliance emerges in its capacity to maintain power transmission despite significant shaft misalignment. This characteristic proves vital in systems requiring independent movement between driving and driven components, such as heavy machinery and transport vehicles.
At its core, the mechanism employs crossed bearing surfaces that facilitate rotational continuity while mitigating stress concentrations. This precise arrangement demands exacting manufacturing standards - even minute deviations can compromise performance and longevity. Regular lubrication and systematic maintenance form the cornerstone of sustainable operation, underscoring why scheduled inspections are non-negotiable for optimal drivetrain health.
What sets universal joints apart is their remarkable angular accommodation range. This versatility shines in unpredictable environments where perfect alignment remains elusive, from off-road vehicles traversing rugged terrain to industrial robots executing complex maneuvers. Such adaptability cements their status as irreplaceable components across mechanical engineering disciplines.
The Mechanics of Angular Compensation: How U-Joints Achieve Flexibility
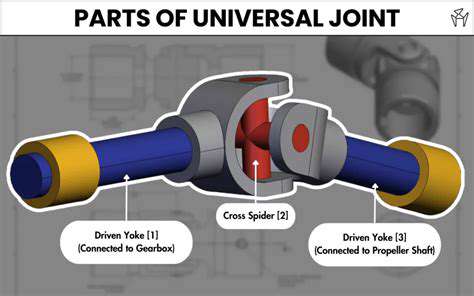
Understanding Angular Velocity
Angular velocity represents the rotational speed about an axis, quantified in radians per second. This fundamental principle governs compensation dynamics in rotating systems. Mastering angular velocity calculations is paramount for rectifying rotational discrepancies in precision systems, from aerospace navigation to robotic articulation. The vector nature of this measurement - encompassing both rotational speed and direction via the right-hand rule - enables engineers to predict torque and angular momentum effects with accuracy.
Types of Angular Compensation Methods
Engineers deploy multiple strategies to counteract angular deviations. Sensor arrays continuously monitor positional data, feeding information to control systems that implement real-time adjustments. Feedforward compensation stands out by proactively neutralizing anticipated disturbances before they impact system performance, proving particularly effective in environments with predictable vibration patterns or inertial forces.
Sensor Integration for Accuracy
Precision compensation hinges on sophisticated sensor fusion. Gyroscopic sensors track rotational velocity while accelerometers map linear forces, creating a comprehensive motion profile. Strategic sensor redundancy enhances reliability in mission-critical applications, with meticulous calibration ensuring measurement integrity across operational parameters.
Mathematical Models for Compensation
From basic kinematic equations to complex differential models, mathematical frameworks enable predictive compensation design. Model fidelity directly correlates with system responsiveness, allowing engineers to simulate responses to diverse operational scenarios during the development phase. These simulations inform compensation algorithms that maintain stability across varying load conditions.
Applications in Various Fields
The reach of angular compensation extends from microscopic surgical robots to orbital satellite arrays. In medical imaging systems, sub-degree compensation enables crystal-clear diagnostic visuals despite patient movement. Industrial CNC systems leverage similar principles to maintain machining precision during high-speed operations, demonstrating the technology's cross-industry relevance.
Applications Beyond Automotive: Universal Joints in Diverse Industries
Beyond the Wheel: Agricultural Machinery
Modern farming equipment relies on universal joints to power implements across undulating terrain. The joint's dynamic articulation permits combine harvesters to maintain consistent power delivery while their headers adjust to crop height variations. This adaptive capability translates directly to yield optimization and reduced mechanical wear, proving invaluable in precision agriculture.
Industrial Robotics and Automation
Six-axis robotic arms exploit universal joints' multi-planar flexibility to execute complex assembly tasks. The components enable seamless torque transfer through articulated wrists performing micron-precision movements. Such dexterity revolutionizes production lines, allowing single robots to handle operations previously requiring multiple specialized machines.
Aerospace Engineering: A Crucial Component
Flight control systems incorporate universal joints to translate pilot inputs into control surface movements. Helicopter rotor systems particularly benefit from these components' ability to accommodate complex three-dimensional forces. Their failure tolerance makes them ideal for flight-critical applications where reliability outweighs all other considerations.
Marine Applications: Seamless Power Transmission
Marine propulsion systems employ hardened universal joints to withstand constant wave-induced vessel motion. The joints' corrosion-resistant designs maintain propulsion efficiency despite the punishing saltwater environment. Their vibration-damping characteristics prove equally valuable in reducing noise signatures for naval applications.
Renewable Energy: A Supporting Role
Horizontal-axis wind turbines utilize universal joints in their yaw mechanisms, allowing nacelles to track wind direction shifts. Solar tracking arrays similarly benefit from the components' ability to accommodate seasonal sun angle variations. This adaptability directly impacts energy capture efficiency, making universal joints unsung heroes in sustainable power generation.
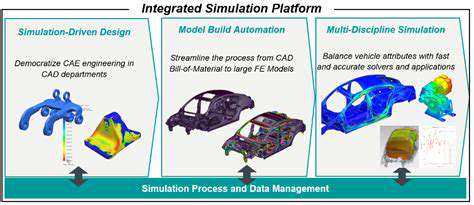
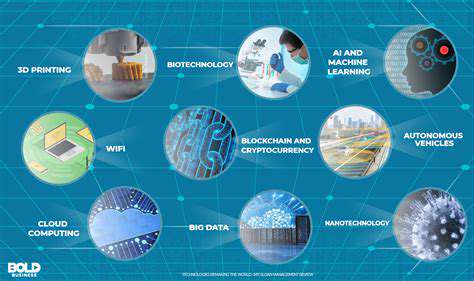