Optimizing Energy Efficiency in Automotive Manufacturing Processes
Minimizing Energy Consumption in Casting Processes
The automotive industry heavily depends on casting processes, which traditionally consume large quantities of energy. To establish more sustainable practices, manufacturers must focus on optimizing these operations. Advanced techniques like die casting, sand casting, and investment casting can significantly reduce energy usage during heating, cooling, and shaping phases. Closed-loop systems for material recovery, when combined with precise temperature regulation, can dramatically cut down on energy waste. Additionally, experimenting with alternative casting materials that require lower melting temperatures could further decrease energy demands during initial processing stages.
Energy-efficient equipment plays a vital role in conservation efforts. Modern furnaces featuring superior insulation and temperature control mechanisms can minimize heat loss substantially. Similarly, innovative mold designs that incorporate thermal retention properties help maintain required temperatures with less energy input. These improvements not only reduce operational costs but also contribute to lowering the carbon footprint of automotive manufacturing. When implemented effectively, such measures can transform casting operations into more environmentally friendly processes.
Improving Energy Efficiency in Welding and Machining Operations
Welding and machining represent substantial energy expenditures in vehicle production. Adopting efficient welding methods such as laser welding or resistance spot welding can decrease the power needed for joining metal components. Fine-tuning welding parameters - including current and voltage settings - helps prevent energy waste while maintaining joint integrity. The introduction of robotic welding systems enhances precision and reduces energy consumption per weld.
For machining operations, utilizing high-performance cutting tools and advanced techniques like high-speed machining (HSM) and multi-axis machining leads to notable energy savings. Regular equipment maintenance and optimization of cutting parameters are fundamental to maximizing machining efficiency. Strategies that improve material removal rates and optimize tool paths can yield significant energy reductions throughout the production cycle. These practices are becoming increasingly important as the industry moves toward more sustainable manufacturing models.
Predictive maintenance programs and real-time energy analytics form critical components of comprehensive efficiency strategies. Variable-speed drives for motors and pumps allow equipment to adjust power consumption based on immediate needs, resulting in substantial energy savings compared to fixed-speed alternatives. Even seemingly minor improvements like energy-efficient lighting and ventilation systems can accumulate meaningful reductions in overall plant energy usage.
Integrating Electric Vehicle (EV) Manufacturing into the Sustainability Framework
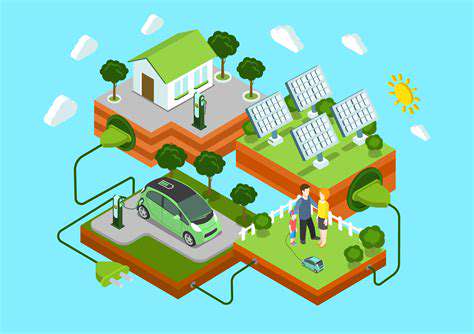
Optimizing Charging Infrastructure
The successful transition to electric mobility depends heavily on establishing comprehensive charging networks. Beyond physical installation, integrating smart technologies enables better demand management and energy optimization. Reliable charging infrastructure directly addresses consumer concerns about vehicle range limitations. Strategic placement of both public and private charging stations requires careful planning and continued investment.
Addressing Range Anxiety
Consumer apprehension about finding available charging stations remains a significant barrier to EV adoption. Transparent communication and dependable charging solutions are crucial for building driver confidence. Providing accurate, real-time information about station locations and charging speeds through mobile applications helps alleviate concerns. This digital support system complements physical infrastructure development.
Enhancing Battery Technology
Breakthroughs in battery technology represent the most promising avenue for improving EV performance. Developing batteries with greater energy density and faster charging capabilities is essential for mass market acceptance. Continued research into advanced battery chemistries, innovative cell architectures, and improved thermal management systems will drive these improvements forward.
Facilitating Policy Support
Government initiatives significantly influence EV market penetration. Financial incentives including tax credits and purchase subsidies make electric vehicles more accessible to consumers. Well-designed policies can dramatically accelerate the transition to cleaner transportation options. Regulatory measures such as stringent emissions standards and production mandates further stimulate industry transformation.
Integrating EV into the Existing Grid
The mass adoption of electric vehicles presents new challenges for power grid management. Smart grid technologies and advanced energy storage solutions are critical for handling increased electricity demand. Implementing strategies to balance charging loads and optimize energy distribution ensures grid stability while accommodating growing numbers of EVs.
Promoting Public Awareness and Education
Consumer education plays a pivotal role in EV adoption. Clear communication about vehicle performance, maintenance requirements, and total cost of ownership helps overcome misconceptions. Comprehensive awareness campaigns highlighting environmental benefits and long-term savings potential can reshape public perception. Developing accessible educational resources empowers consumers to make informed decisions about transitioning to electric mobility.