Case Study 2: Volkswagen's Commitment to Sustainability in Manufacturing Plants
Volkswagen's Environmental Initiatives: A Holistic Approach
When examining Volkswagen's manufacturing plants, one quickly notices their unwavering dedication to sustainability transcends mere compliance with regulations. The automaker has woven environmental consciousness into every thread of its operations, creating a tapestry of initiatives that address energy use, material sourcing, and waste reduction. Their factories hum with renewable energy systems while recycling programs divert tons of material from landfills annually.
What truly sets Volkswagen apart is their supply chain transformation. Rather than focusing solely on their own facilities, they've implemented rigorous sustainability standards for all suppliers. This creates a ripple effect throughout the industry, as partners upgrade equipment and processes to meet Volkswagen's exacting environmental criteria. The result? A manufacturing ecosystem where sustainability becomes the baseline rather than the exception.
Operational Efficiency and Resource Optimization
Walk through any Volkswagen plant and you'll witness a masterclass in efficiency. Every kilowatt-hour matters - from LED lighting that automatically adjusts to natural light levels to heat recovery systems that capture wasted thermal energy. Their waste management goes beyond simple recycling; it's a sophisticated materials recovery operation where byproducts from one process become inputs for another.
The company's digital transformation has yielded remarkable environmental benefits. Advanced sensors monitor energy use in real-time, while predictive algorithms optimize material flows. This technological edge allows Volkswagen to achieve unprecedented precision in resource allocation, minimizing waste without sacrificing productivity. Their factories increasingly resemble living organisms, constantly adapting to maintain perfect environmental equilibrium.
One particularly innovative approach involves using artificial intelligence to simulate production scenarios. These digital twins allow engineers to test thousands of configurations virtually, identifying the most resource-efficient methods before implementing them physically. This forward-thinking application of technology demonstrates how Volkswagen continues to push the boundaries of sustainable manufacturing.
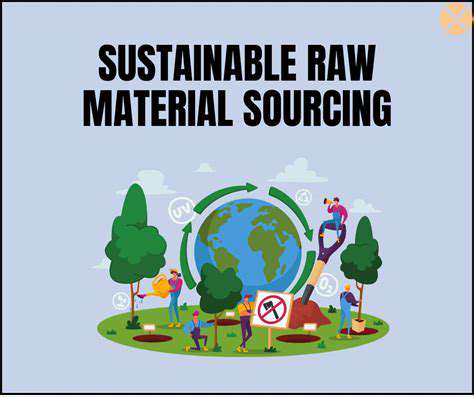
Future Trends and Challenges
Emerging Battery Technologies
The battery revolution continues at breakneck pace. While lithium-ion dominates today, researchers are making breakthrough progress on solid-state designs that promise greater safety and energy density. These next-generation power sources could dramatically extend EV range while reducing charging times to minutes rather than hours.
Parallel developments in alternative chemistries like lithium-sulfur present intriguing possibilities. Though currently hampered by durability issues, successful commercialization could yield batteries with twice the energy capacity of current models. The race to perfect these technologies represents one of the most exciting frontiers in sustainable transportation.
Sustainable Material Sourcing
Automakers face mounting pressure to address the environmental and ethical concerns surrounding rare earth metals. Forward-thinking companies are exploring everything from deep-sea mining alternatives to advanced recycling techniques that can recover 95%+ of battery materials. Some are even redesigning components to eliminate problematic elements entirely.
Integration of Renewable Energy Sources
The factories of tomorrow won't just use renewable energy - they'll generate it. Solar-integrated roofs, wind turbines, and geothermal systems are becoming standard features at leading manufacturing sites. More ambitious projects include microgrid systems that allow plants to operate independently during outages while feeding surplus clean energy back to local communities.
Optimized Manufacturing Processes
Next-generation manufacturing combines digital precision with sustainable principles. Smart sensors optimize energy use in real-time, while machine learning algorithms identify waste reduction opportunities humans might miss. The result? Factories that continuously evolve toward greater efficiency with each production cycle.
Advancements in Electric Vehicle Design
EV designers are pushing boundaries with innovative approaches to aerodynamics and lightweighting. New composite materials and 3D-printed components allow for structures that are simultaneously stronger and lighter. These advancements translate directly to greater range and efficiency, making electric vehicles more practical for mainstream consumers.
Policy and Infrastructure Development
The transition to sustainable automotive production requires more than corporate initiative. Governments must create frameworks that incentivize green manufacturing while investing in the charging infrastructure needed to support mass EV adoption. Forward-looking policies can accelerate the industry's transformation, creating a virtuous cycle of innovation and environmental benefit.