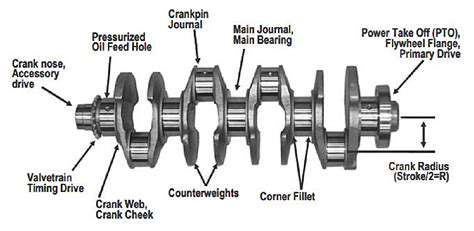
Maintaining Your Crankshaft Position Sensor
Understanding the Crankshaft Position Sensor
The crankshaft position sensor (CKP sensor) is a crucial component in internal combustion engines, playing a vital role in accurately determining the crankshaft's rotational position. This information is critical for the engine's management system to control ignition timing, fuel injection, and other critical functions. Without precise information from the CKP sensor, the engine would not function properly, potentially leading to misfires, poor performance, or even complete engine failure.
Its fundamental function is to provide a precise electrical signal representing the crankshaft's position. This signal is then interpreted by the engine control module (ECM) to synchronize various engine operations. The accuracy of this signal is paramount for optimal engine performance and efficiency.
Troubleshooting Common CKP Sensor Issues
Several issues can lead to problems with the CKP sensor, impacting the engine's operation. One common problem is a faulty sensor itself, which may be due to a damaged wire harness or a component failure within the sensor. Another potential issue is a loose or corroded connection. If these are not addressed, the engine may exhibit irregular idling, rough acceleration, or even complete stalling.
A faulty CKP sensor can also lead to problems with the engine's overall performance, such as reduced power output and difficulty in starting. Checking for loose connections, inspecting the wiring, and ensuring the sensor is properly installed can often resolve these issues.
Inspection and Maintenance Procedures
Routine inspection and maintenance of the CKP sensor are vital for ensuring its longevity and optimal performance. This includes checking for any visible damage to the sensor housing, wiring, or connections. Inspecting the wiring harness for signs of wear or damage is also important, as damaged wires can lead to intermittent issues with the sensor signal.
Cleaning the sensor's contacts and ensuring proper connections are crucial for accurate signal transmission. Regularly checking the sensor's electrical resistance against manufacturer specifications can help identify potential problems early on.
The Impact of a Malfunctioning CKP Sensor
A malfunctioning crankshaft position sensor can lead to a range of issues, significantly impacting the engine's performance and reliability. One common symptom is a rough or erratic idle, making the engine difficult to control. Furthermore, the engine may experience misfires, especially during acceleration, resulting in poor performance and reduced fuel economy.
In more severe cases, a faulty sensor can cause the engine to stall or fail to start. Addressing these problems promptly is crucial to prevent further damage and maintain the engine's optimal performance.
Sensor Replacement and Repair Considerations
Replacing a faulty CKP sensor is often necessary to restore proper engine function. The process involves disconnecting the old sensor, carefully removing it from its housing, and installing the new sensor, ensuring a secure and proper fit. It's important to follow the manufacturer's instructions carefully throughout the replacement process, as improper installation can lead to further problems.
While repair is sometimes possible, replacing the sensor is often the most effective solution, especially if the problem is related to internal component failure. Ensuring the correct sensor type is installed and the wiring connections are secure is essential for optimal performance.
Diagnosis and Testing Procedures
Accurate diagnosis is crucial for identifying a malfunctioning crankshaft position sensor. Diagnostic tools, such as a scan tool or multimeter, can be used to assess the sensor's output signal and compare it against established specifications. By comparing the sensor's output with expected values, technicians can pinpoint the source of the problem and determine whether the sensor itself is faulty or if there are issues with the wiring or connections.
Thorough testing procedures are essential to ensure accurate diagnosis. This may involve checking the sensor's resistance, verifying the signal output, and troubleshooting any potential wiring issues. Proper testing ensures that the correct diagnosis is made, leading to an effective and efficient repair solution.