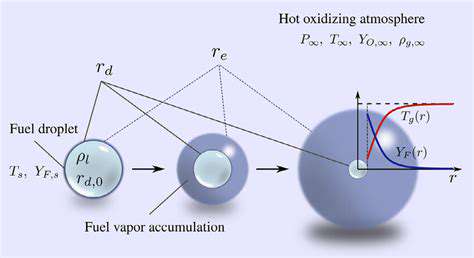
Components of the Fuel Evaporation System
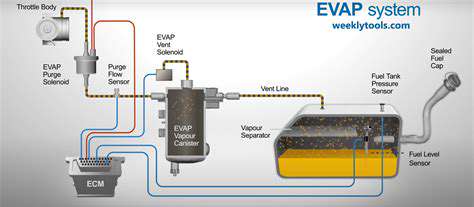
Fuel Tank Design
Fuel tank design plays a pivotal role in controlling evaporation rates. Tanks featuring smooth, rounded surfaces reduce atmospheric exposure, effectively limiting evaporation potential. High-quality seals and venting mechanisms are equally important to contain fuel vapors and prevent unnecessary losses.
Material selection for tank construction significantly influences performance. Advanced alloys and specialized polymers that resist fuel vapor permeation are increasingly preferred. These materials create an effective barrier, minimizing molecular migration through tank walls.
Ambient Temperature and Humidity
Environmental conditions dramatically affect fuel behavior. Elevated temperatures energize fuel molecules, accelerating their transition to vapor phase. Regions with consistently warm climates typically experience more pronounced evaporation issues.
Humidity levels create an interesting counterbalance. Moisture-rich air leaves less capacity for fuel vapors, somewhat suppressing evaporation rates. This interaction between temperature and humidity creates complex regional variations in fuel loss patterns.
Fuel Composition
The molecular makeup of fuel directly determines its evaporation characteristics. Light fractions with lower boiling points vaporize more readily than heavier components. Accurate knowledge of fuel formulation proves essential for developing effective evaporation control strategies.
Different fuel types exhibit distinct behaviors. Gasoline's relatively light composition makes it more prone to evaporation compared to diesel. These fundamental differences necessitate tailored approaches for each fuel category.
Ventilation Systems
Properly engineered ventilation serves as a critical control mechanism. These systems either safely contain or redirect fuel vapors. Well-designed ventilation prevents dangerous vapor accumulation while maintaining proper tank pressurization.
Balancing pressure differentials requires precise engineering. The system must allow controlled vapor release without permitting fuel expulsion, creating a delicate equilibrium between safety and efficiency.
Storage Duration
Time significantly impacts cumulative evaporation losses. Extended storage periods compound exposure effects. Container integrity becomes increasingly critical as storage duration lengthens.
Optimal storage practices involve maintaining stable, moderate environmental conditions. Regular monitoring helps identify potential issues before they lead to significant fuel degradation or loss.
Tank Coatings and Sealants
Specialized barrier treatments provide additional protection. High-performance coatings create molecular barriers that dramatically reduce vapor transmission.
Proactive maintenance of these protective layers ensures continued effectiveness. Routine inspections can identify wear before it compromises the coating's protective qualities.
Environmental Factors
Multiple external elements influence evaporation dynamics. Solar radiation heats tank surfaces, while wind accelerates vapor dispersion. These factors interact in complex ways that require careful consideration during system design.
Comprehensive environmental analysis helps predict real-world performance. Understanding these interactions enables more accurate modeling of evaporation behavior across different operating conditions.
The Role of Vapor Recovery Systems
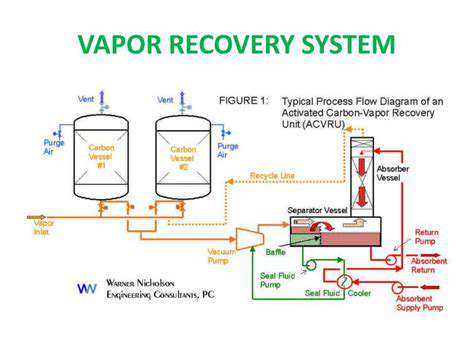
Vapor Recovery System Fundamentals
Modern vapor recovery technology represents a critical solution for VOC management across multiple industries. These sophisticated systems capture and process volatile compounds before they can enter the atmosphere. Effective implementation delivers both environmental protection and operational benefits. The technology demonstrates how industrial processes can align with sustainability goals while maintaining productivity.
The core mechanism involves specialized equipment that intercepts and condenses vapor streams. This process transforms potential pollutants into recoverable liquids. Industry-specific adaptations ensure optimal performance across diverse applications. From petroleum operations to chemical manufacturing, customized solutions address unique operational challenges.
Modern systems typically incorporate multiple processing stages. Initial collection gives way to condensation and eventual product recovery. This integrated approach maximizes resource utilization while minimizing environmental impact. Continuous innovation improves both efficiency and applicability across different industrial contexts.
Vapor Recovery System Applications and Benefits
Industrial adoption spans numerous sectors with high VOC potential. Petroleum operations capture valuable hydrocarbons, while chemical plants recover solvents. This dual benefit of environmental protection and resource conservation drives widespread implementation.
The economic case for vapor recovery continues to strengthen. Material recovery offsets operational costs while regulatory compliance avoids potential penalties. These financial considerations complement the environmental advantages, creating compelling business cases for adoption.
Public health improvements represent another significant benefit. Reduced VOC emissions contribute to better air quality, particularly in industrial regions. Worker safety also improves through reduced exposure to potentially harmful vapors.
Future Trends in Fuel Evaporation System Design
Improving Efficiency through Miniaturization
Component miniaturization drives significant efficiency gains. Compact designs maintain performance while reducing weight and space requirements. This evolution supports broader vehicle efficiency goals and enables more flexible system integration.
Advanced Materials and Coatings
Material science innovations deliver enhanced durability and performance. New composites withstand extreme conditions while specialized coatings optimize thermal characteristics. Sustainable material development aligns with broader environmental objectives.
Integration with Vehicle Control Systems
Smart system integration enables real-time performance optimization. Advanced ECUs adjust evaporation parameters based on multiple operational variables. This connectivity improves both efficiency and emissions performance across diverse operating conditions.
Enhanced Sensor Technology
Precision monitoring technologies provide unprecedented system visibility. Advanced sensors deliver real-time data for precise control adjustments. This capability supports more responsive and efficient system operation.
Focus on Emissions Reduction
Regulatory pressures drive continuous emissions improvement. Innovative designs target VOC reduction through multiple technical approaches. These developments help manufacturers meet increasingly stringent environmental standards.
Sustainable Materials and Manufacturing Processes
Lifecycle environmental impact receives growing attention. Recycled materials and cleaner production methods reduce overall footprint. This holistic approach considers environmental impact from design through disposal.
Predictive Maintenance and Diagnostics
Data-driven maintenance strategies improve system reliability. Advanced analytics identify potential issues before they cause operational disruptions. This proactive approach maximizes uptime while minimizing maintenance costs.