Crucial Role of Coolant System Pressure in Engine Health
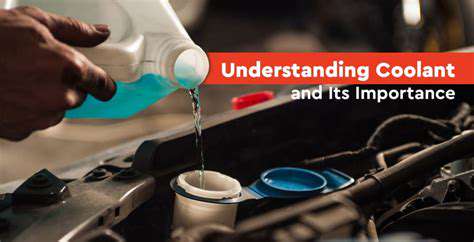
Importance of Proper Coolant System Preparation Before Operation
The initial setup of a coolant system is critical for ensuring peak performance and extended machinery life. Meticulous preparation includes inspecting all components for leaks, confirming fluid levels, and removing any contaminants. Overlooking these steps often results in system malfunctions and expensive repairs later on. Conducting routine checks before operation allows for early problem detection, reducing downtime and maintaining efficiency. Operators must adhere strictly to manufacturer instructions during this stage.
Beyond physical examinations, testing coolant quality before use is equally important. This verifies proper viscosity, pH balance, and absence of damaging impurities. Taking this preventive measure helps avoid corrosion, blockages, and overheating issues that might weaken the system. Proper preparation also includes adjusting sensors and gauges to guarantee accurate operational readings. In essence, thorough pre-start procedures establish the groundwork for dependable and effective Coolant System performance.
Key Components to Check During System Pre-Start
Prior to activating the coolant system, technicians should examine essential parts like pumps, valves, and filters. Ensuring pumps run smoothly without unusual sounds helps prevent sudden failures. Clean, unobstructed filters are necessary to maintain consistent coolant flow and filtration. Any visible wear or damage must be fixed immediately to prevent contamination or system breakdown.
Inspecting the coolant reservoir to confirm proper fluid levels is another vital step. Correct levels are crucial for maintaining pressure and circulation. Additionally, checking hoses and connections for leaks ensures system airtightness. These straightforward but critical inspections greatly lower the risk of operational issues caused by avoidable problems.
Steps for Ensuring System Safety Before Use
Safety is the top priority when preparing a coolant system for operation. A complete safety check should include verifying that all safety valves and pressure relief devices are properly installed and functional. This prevents hazardous pressure buildup that could damage equipment or cause accidents. Operators should also ensure emergency shut-off mechanisms are easily accessible and working. Clear labeling and signage enhance safety awareness among staff.
Before starting the system, running a dry test to observe flow and spot irregularities is recommended. Wearing appropriate personal protective equipment (PPE) is mandatory during inspections and tests. Keeping the work area free of hazards minimizes risks associated with high-pressure fluids or hot surfaces during startup.
Common Mistakes to Avoid During Coolant System Pre-Start
A frequent error is rushing through pre-start procedures without thorough inspections, leading to missed leaks or damaged parts. Neglecting coolant quality checks can cause corrosion or inefficiency, resulting in long-term harm. Following a detailed checklist ensures all aspects are properly addressed.
Another common oversight is failing to calibrate sensors and gauges correctly, which produces inaccurate readings during operation. This may lead to poor decisions or ignored warning signs. Lastly, disregarding manufacturer guidelines for coolant types and maintenance schedules can drastically shorten system lifespan and effectiveness. Diligence during the pre-start phase saves time and money over time.
Benefits of Thorough System Pre-Check
A comprehensive pre-start check boosts overall system reliability, cutting unexpected downtime and repair costs. Proper preparation ensures the system operates within specified limits, optimizing heat transfer and cooling performance. This proactive strategy also prolongs the life of critical components by preventing corrosion and wear from impurities or incorrect fluid levels. Moreover, it creates a safer work environment by reducing accident risks linked to system failures.
Investing time in detailed pre-start inspections improves system monitoring as calibrated sensors provide precise data for better decision-making. Overall, thorough pre-operation procedures are a key part of maintenance that contribute to operational excellence and safety in machinery reliant on coolant systems.
Detecting Leaks and Potential Problems Early
Identifying Signs of Coolant Leaks Before They Cause Serious Damage
One of the best ways to prevent major cooling system failures is by spotting early signs of coolant leaks. Common indicators include a persistent coolant smell inside the vehicle, visible puddles under the car, or sudden drops in coolant levels. Paying attention to these signs helps address issues before they become costly repairs or engine damage.
Another important sign is white smoke or steam from the engine bay, especially after running. This often means coolant is leaking onto hot engine parts, which can cause overheating if ignored. Regularly checking hoses and radiator components for cracks or corrosion can also catch leaks early, saving time and money.
Monitoring Temperature and Pressure Readings for Early Detection
Regularly watching your vehicle’s temperature gauge is key for early problem detection. Unusual temperature rises, especially sudden or frequent ones, may indicate a coolant leak or blockage. Sudden spikes should prompt immediate inspection for leaks or faulty parts.
Maintaining proper system pressure is also vital. Modern vehicles have pressure caps to regulate this; malfunctioning or improperly installed caps can cause leaks or steam. Regularly checking cap integrity and ensuring tight seals on radiators and hoses prevents pressure-related issues from worsening.
Implementing Routine Maintenance to Detect Problems Early
Scheduled maintenance is essential for early coolant system issue detection. During routine checks, technicians inspect hoses, clamps, radiators, and water pumps for wear or leaks. Flushing the system and replacing coolant at recommended intervals prevents corrosion and buildup that can cause leaks or clogs.
Using diagnostic tools like pressure testers or leak detectors enhances early problem identification. These tools find leaks invisible to the eye, ensuring quick fixes. Consistent maintenance and early detection greatly extend cooling system life and keep engines running at optimal temperatures.
Preventing Overheating and Engine Damage
Regular Coolant System Maintenance Ensures Optimal Engine Performance
Maintaining the coolant system is crucial for keeping the engine within the ideal temperature range. Over time, coolant degrades, reducing heat transfer efficiency and increasing overheating risks. Regular inspections and fluid replacements prevent blockages and maintain circulation, protecting engine parts from thermal stress. Skipping these tasks can lead to expensive repairs and shorter vehicle life.
Checking for leaks, corrosion, and worn hoses during routine maintenance can catch problems before they worsen. Ensuring the right antifreeze-to-water ratio is also vital for system effectiveness in all weather. Proper coolant system care is a proactive way to shield your engine from preventable overheating damage.
Signs of Coolant System Failure and When to Seek Professional Help
Recognizing early signs of coolant system issues can prevent overheating and major repairs. Common indicators include the temperature gauge rising abnormally, steam or coolant leaks under the car, and a sweet antifreeze smell inside or outside. If your heater works poorly, it might mean low coolant flow, signaling a problem.
If you notice these symptoms, have a professional inspect your cooling system immediately. Delaying can cause overheating, warped cylinder heads, or complete engine failure. Regular check-ups and early fixes keep your vehicle reliable and prevent costly coolant system damage.
Preventative Measures to Avoid Overheating During Extreme Weather
Extreme weather adds challenges to maintaining a healthy coolant system. To prevent overheating in heat, ensure your radiator works well and coolant levels are correct. The right antifreeze mix protects against freezing in cold and boiling in heat.
A high-quality radiator cap and proper airflow improve heat dissipation. Monitor the temperature gauge more often in extreme weather and avoid heavy engine loads at peak temperatures. These steps are key to engine integrity and avoiding overheating in harsh conditions.
Upgrading Your Cooling System for Better Heat Management
For high-performance vehicles or those in demanding conditions, cooling system upgrades improve heat management and engine durability. Modern parts like high-capacity radiators, electric fans, and performance hoses dissipate heat better and reduce stress-related overheating risks.
Some owners choose specialized coolants for higher temperatures or better corrosion resistance. Automotive specialists can recommend suitable upgrades based on your driving habits and vehicle specs. These improvements can greatly extend engine life and boost reliability by ensuring optimal temperature control.
Ensuring Efficient Heat Transfer and System Integrity
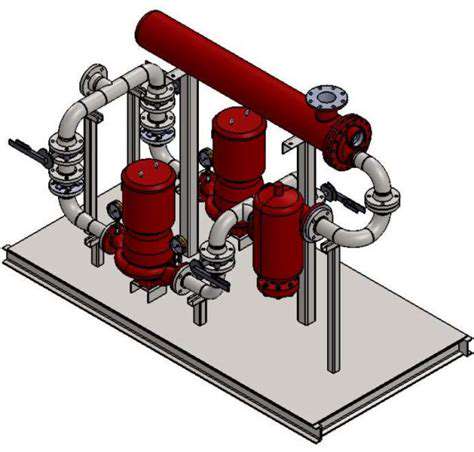
Optimizing Material Selection for Heat Conductivity
Choosing the right materials is key for efficient heat transfer. High-thermal-conductivity materials like copper and aluminum are ideal because they enable rapid heat flow. These materials help devices perform better by reducing temperature differences and improving efficiency. Understanding thermal properties helps design systems that maximize heat transfer while minimizing energy loss.
However, material selection also depends on cost, durability, and compatibility. While copper conducts heat well, it may be pricier than aluminum, which still performs well. Engineers must weigh these factors to create affordable, reliable heat transfer solutions.
Designing for Optimal Surface Area and Contact
Maximizing contact surface area between heat sources and transfer mediums boosts heat exchange efficiency. Designs often use fins, plates, or extended surfaces to increase heat transfer area. Secure component contact minimizes thermal resistance, crucial for fast heat movement. Tight connections prevent gaps that hinder heat flow.
Innovations like corrugated surfaces or layered structures can significantly improve heat transfer rates in compact systems where space is limited.
Implementing Effective Heat Transfer Fluids
Choosing the right heat transfer fluids is vital for efficient thermal management. Fluids like water, glycol mixtures, or specialized oils are selected based on temperature ranges and system needs. These liquids absorb and move heat well due to their high specific heat capacities and thermal conductivities. Proper flow rates and circulation methods further optimize performance.
Advanced fluids like nanofluids—liquids with nanoparticles—offer enhanced thermal properties. Using these can significantly improve heat transfer system efficiency, especially in high-performance applications like electronics cooling.
Utilizing Advanced Heat Exchanger Technologies
Modern heat exchangers focus on maximizing efficiency while minimizing size and energy use. Techniques like counter-flow configurations, shell-and-tube designs, and plate heat exchangers achieve these goals. These designs improve temperature gradients and enhance fluid heat exchange. Regular maintenance and cleaning maintain efficiency over time.
Emerging technologies like microchannel heat exchangers and 3D printing enable more compact, efficient solutions. These innovations allow heat transfer system integration in space-limited environments like aerospace or portable electronics.
Monitoring and Controlling System Performance
Effective heat transfer systems need continuous monitoring for peak efficiency. Sensors and data systems track temperature, flow rates, and pressure in real-time. This data helps spot issues early, like blockages or leaks, that could affect performance. Automated controls can adjust flow rates or coolant temperatures dynamically to optimize heat transfer under changing conditions. These controls maintain efficiency and prevent failures.
Predictive maintenance technologies extend component life. Analyzing operational data allows proactive scheduling, reducing downtime and ensuring consistent thermal management.
The Importance of Professional Testing and Timely Repairs
Ensuring Safety Through Accurate Diagnostics
Professional testing is crucial for accurately diagnosing issues in complex systems. Skilled technicians use specialized tools to find problems that visual inspections might miss. Precise diagnosis prevents failures that could create hazards, ensuring operator and user safety.
Accurate diagnostics also prevent unnecessary repairs by identifying only faulty components, saving time and money. Early correct identification makes it easier to implement solutions before small issues become major problems.
Maintaining Equipment Efficiency and Longevity
Regular professional testing keeps equipment performing optimally, ensuring efficiency and lower energy use. Over time, parts wear out or misalign, reducing performance and raising costs. Timely repairs based on test results restore peak condition.
Prompt fixes significantly extend machinery life. Proper maintenance reduces unexpected breakdowns that can be disruptive and expensive, protecting your equipment investment.
Preventing Costly Future Repairs
Proactive testing and maintenance catch potential problems before they become serious. Regular technician assessments spot early wear or damage that might otherwise go unnoticed. Early fixes prevent escalation into costly repairs or replacements.
Timely professional repairs save money long-term. This preventive approach minimizes downtime, lowers emergency repair costs, and keeps systems running smoothly.
Complying With Industry Standards and Regulations
Many industries require regular testing and maintenance to meet safety and operational standards. Professional testing ensures compliance, avoiding legal penalties and shutdowns. It also shows commitment to safety and quality, enhancing company reputation.
Certified professional inspections and repairs help companies stay current with evolving standards. Proactive compliance protects workers and consumers while reassuring stakeholders and regulators.
Enhancing Reliability and Customer Satisfaction
Well-maintained equipment is more reliable, directly improving customer satisfaction. Fewer disruptions or failures build client confidence. Reliable operation ensures timely service or product delivery, fostering trust and loyalty.
Professional testing and repairs build a reputation for quality and dependability. This can set a business apart in competitive markets, attracting and retaining customers through demonstrated excellence.
Utilizing Advanced Technologies for Better Results
Modern testing uses digital diagnostics, thermal imaging, and AI analysis for more accurate, comprehensive assessments. These technologies find issues traditional methods might miss, leading to better repairs.
Advanced tools improve diagnostic accuracy and speed, reducing downtime. Staying current with technology ensures maintenance practices remain effective and aligned with industry best practices.
Building a Culture of Preventative Maintenance
Regular professional testing and timely repairs create a proactive maintenance culture. This approach focuses on prevention over reaction, emphasizing early intervention. It encourages staff to prioritize maintenance as key to operational success.
Over time, this culture reduces unexpected failures, increases uptime, and promotes safety. Investing in routine testing and repairs shows long-term commitment to quality, reliability, and safety, benefiting the entire organization.