The recovery of metals from spent EV batteries relies heavily on hydrometallurgical techniques, where aqueous chemistry plays a pivotal role. Selective dissolution using carefully formulated chemical solutions enables the separation of nickel, cobalt, and manganese from battery waste. Various leaching agents show different affinities for specific metals - sulfuric acid works well for cobalt extraction while hydrochloric acid may be preferred for certain nickel compounds. The process requires meticulous control of operating conditions; temperature fluctuations of just 5°C can alter dissolution rates by up to 15%, and pH must remain within strict parameters to prevent unwanted precipitation.
Battery chemistry significantly impacts leaching efficiency. Nickel-cobalt-manganese (NCM) cathodes demand different treatment than lithium iron phosphate (LFP) variants. Recent studies show that adding reducing agents like hydrogen peroxide can boost lithium recovery by 30% in NCM batteries. Environmental safeguards are non-negotiable - modern plants employ closed-loop water systems and neutralization tanks to treat effluent before discharge.
Pyrometallurgy: High-Temperature Processes
Thermal treatment methods harness extreme heat (often exceeding 1200°C) to liberate metals from their matrices. In furnace operations, carbon acts as both fuel and reducing agent, converting metal oxides to elemental form. The process excels at handling mixed battery streams where mechanical separation proves difficult. Aluminum casings melt and separate from copper windings, while valuable metals alloy in the molten phase.
Modern smelters now capture up to 98% of particulate emissions using electrostatic precipitators and baghouse filters. The slag byproduct finds use in construction materials after proper vitrification. Energy recovery systems can repurpose waste heat for district heating, improving overall efficiency. However, the carbon footprint remains substantial - a typical batch process emits approximately 2.5 tons CO₂ per ton of treated batteries.
Physicochemical Methods: Novel Approaches
Cutting-edge separation technologies are rewriting the recycling playbook. Ion-exchange resins demonstrate remarkable selectivity - certain chelating polymers can extract over 99% of cobalt while rejecting 95% of impurities. Membrane technologies show particular promise; electrodialysis setups with selective ion-exchange membranes achieve lithium purity levels exceeding 99.9%. These methods operate at near-ambient temperatures, slashing energy use by up to 70% compared to thermal processes.
Materials Characterization and Optimization
Precise analysis drives recycling efficiency. X-ray diffraction reveals crystal structure changes during processing, while ICP-MS (Inductively Coupled Plasma Mass Spectrometry) detects trace elements down to parts-per-billion levels. Advanced SEM-EDS systems provide micron-scale elemental mapping, showing exactly where valuable metals concentrate in battery components. This data informs process adjustments in real-time - if manganese levels in the leachate spike unexpectedly, operators can immediately modify pH to optimize selectivity.
Economic and Environmental Considerations
The recycling equation balances multiple factors. Current nickel prices around $20/kg make its recovery economically compelling, while lithium at $15/kg requires efficient processing to remain viable. Life-cycle assessments reveal that proper recycling can reduce battery production's carbon footprint by 40%. Waste minimization strategies are critical - modern facilities now recover over 95% of process water and convert 85% of solid residues into saleable byproducts.
The Future of Sustainable Battery Recycling
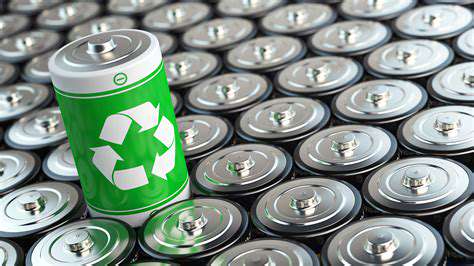
Advancements in Battery Materials
The materials revolution is transforming energy storage. Solid-state electrolytes using ceramic or polymer matrices eliminate flammable liquids while enabling 50% higher energy densities. Researchers at leading institutions are testing iron-based cathodes that could reduce costs by 60% compared to nickel-cobalt systems. Silicon-graphite composite anodes now demonstrate 400+ cycle lives while offering 30% greater capacity than conventional designs.
Technological Innovations in Battery Design
Structural innovations are breaking traditional form factors. 3D-printed battery architectures allow customized shapes for electric aircraft and wearable devices while improving thermal management. Bipolar stacking designs reduce internal resistance, boosting power density by 25%. Smart batteries with embedded sensors now provide real-time degradation data, enabling predictive maintenance and optimized second-life applications.
Environmental Impact and Sustainability
The industry is moving toward closed-loop systems where 95% of battery mass gets reclaimed. New solvent-free electrode manufacturing cuts VOC emissions by 80%, while dry room energy use has halved through advanced dehumidification tech. Bioleaching using specially cultured bacteria shows potential to extract metals at 40°C instead of 80°C, dramatically lowering energy needs.
Economic Considerations and Market Trends
Government mandates are reshaping the landscape - the EU's new regulations require 70% battery material recovery by 2030. Recycling startups attracted over $2 billion in venture funding last year alone. Economies of scale are kicking in - large recycling plants now process batteries at $5/kg, down from $15/kg five years ago. The secondary battery materials market is projected to reach $25 billion by 2028.
Future Applications and Societal Impact
Next-generation storage will transform energy access. Modular battery systems are bringing reliable power to off-grid communities, with pilot projects showing 90% reliability at half the cost of diesel generators. Vehicle-to-grid technology could turn EV fleets into distributed storage networks, potentially supplying 10% of peak urban demand. In healthcare, flexible batteries enable revolutionary wearable monitors that track vital signs continuously for weeks.